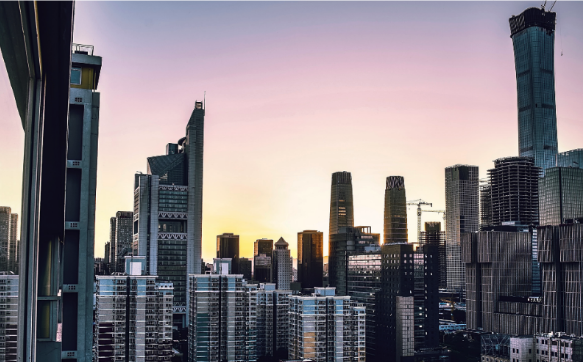
When completing a project in our industry, quality control has to be a top priority for the management team. If corners are cut, you risk falling short on your deliverables – Or worse. Team members may be put into unnecessarily hazardous situations. That’s where hold points come in. They’re predetermined moments during the timeline of the project where work is required to be stopped so that a site inspection can take place.
We’ve listed out three ways effective construction managers can leverage hold points to better accomplish their goals:
1. Timely Verification
Hold points can be extremely valuable when established for verification of construction quality on parts of the project which can’t readily be inspected later on.
A good example of this is to put a hold on concrete pouring activities until a supervisor or certified inspector has the chance to review the steel reinforcement first. Because it would be nearly impossible to go back after the concrete is poured and make sure the infrastructure was safe and sound, it makes sense to stop work in the interest of safety, and continue operations once it’s confirmed that everything is in order.
2. High-Cost Implications
Another reason for using a hold point on a project is when there is a phase with high enough cost implications that it could derail operations if not done correctly. Think of this as a failsafe.
You don’t often have the opportunity to try again without some sort of repercussion. If the issue is big enough, it has the potential to create serious setbacks. Improperly executing a task like laying the foundation can lead to major errors in later phases of construction.
Tip: A great way to mitigate this risk is to place a hold point prior to any additional actions being taken on the project so that leadership can ensure that the foundation is up to code before risking spending money on the rest of the build.
3. Ensuring Completion
Construction managers can also leverage a hold point during a project is to use it as a checkpoint.
Some crews tend to be over eager when trying to complete a build. They may skip important steps in their haste to meet employer deadlines. Sometimes, this means that the second stage of construction is started before everything in the first stage is complete. Placing a hold point to verify that stage one is finished in its entirety before stage two can begin encourages the team to work together and tie up any remaining loose ends. If not, things come to a complete halt.
It’s a quality control method which is highly effective when used on complicated projects!
Making Your Next Quality Control Plan
We hope that this information was helpful and that it will help you strategically map out your next quality control plan. If you need an example of an effective Quality Control Plan, we highly encourage you to take a look at our templates.
About Gadzoom
Gadzoom enables you to generate important documents in minutes, giving you the freedom to run and manage your business without all the headaches that come with administrative responsibilities. Our company was born to make construction document management as streamlined as possible. Create a variety of government compliant safety and administrative documents at the touch of a button. If you’re interested in learning more, visit our site today.