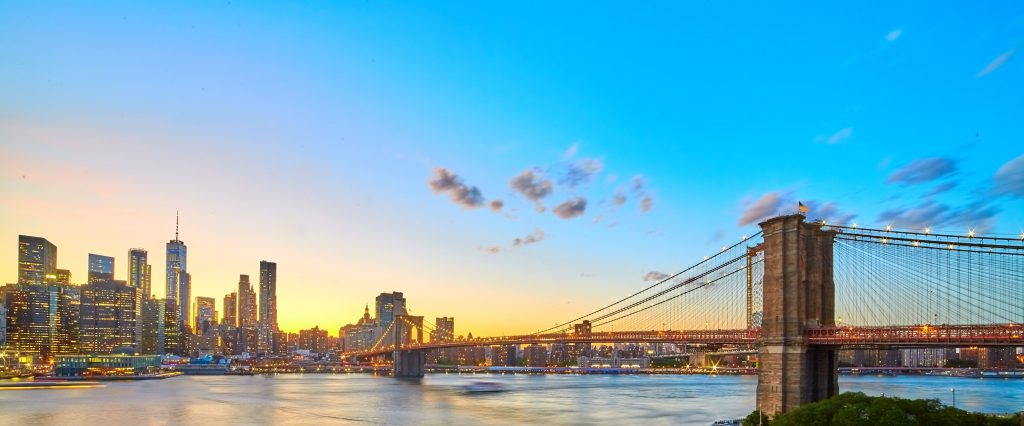
The contractor's quality management program is a written document defining the contractor's processes, practices, and procedures, which are to ensure the project's quality requirements are met or exceeded.
Managing it properly takes a dedication to the client, and an understanding of your team’s strengths and weaknesses. Here are 4 tips from Gadzoom to help construction managers achieve the standards spelled out for each particular quality control program document.
Tip #1 - Identify Barriers to Success
Quality control isn’t always about catching errors in the work your employees and subcontractors are doing. It also pertains to identifying and preparing for barriers to the project’s success.
For example, these can include shortages in labor, delays in procurement, and unique environmental challenges stemming from the location of your job site. Additionally, with a regular turnover of key positions in our industry, subcontractors may fall through, and the weather may impact work.
A good quality control manager is thorough in finding these potential issues and building in contingencies to make sure that the project is finished on time and up to the standards expected from the client.
Tip #2 - Keep Your Personnel Informed
It’s one thing to set expectations on paper, but it’s a totally different challenge to achieve 100% buy-in from all members of yours and your subcontractors’ field team. Supervisors need to dedicate themselves to earning the respect of their crews and setting the tone early that anything less than the highest quality of work will not be tolerated.
It takes grit, finesse, and the ability to connect with your employees so that you’re all on the same page. Furthermore, making sure that each member of your team is properly trained and prepared to address challenges as they arise will make your job that much easier. After all, we’re really in the business of risk management.
Tip #3 - Do Regular Testing and Inspections
Regularly testing and inspecting the quality of work on a project is an effective way to make sure you won’t have any unexpected surprises at completion.
During work on each phase of the job, it’s important to set up hold points so that managers have the opportunity to review and evaluate the level of quality for any particular deliverable. Construction elements like soil compaction and strength of concrete are difficult to make right should a major issue emerge down the road, so it’s crucial to spot and address warning signs for those errors as early as possible.
Related Article: 3 Subjects to Consider In An Environmental Protection Plan
Tip #4 - Make Sure You Are Planning Properly
Identifying barriers, managing your team, and regularly testing for quality of the job all start with a well-built Quality Control Plan. With Gadzoom, we make it easy to generate construction documents that are proven to work. We understand contractors because we are contractors, and our platform lets you quickly and easily edit plans at any time – Helping you stay on track for any project.
If the quality of the work ever comes into question, you risk losing thousands of dollars on the project – or worse – having to start from scratch. That being said, everyone from the bottom of the organizational chart to upper management has a stake in making your quality control program go smoothly.
About Gadzoom
Gadzoom enables you to generate important documents in minutes, giving you the freedom to run and manage your business without all the headaches that come with administrative responsibilities. Our company was born to make construction document management as streamlined as possible. Create a variety of government compliant safety and administrative documents at the touch of a button. If you’re interested in learning more, visit our site today.